Total Quality Systems, Inc. provides a wide array of engineering services to Government and private industry customers. Our Associates are diverse in experience and capabilities. Below are some examples of the types of services that we provide. Please contact us to see how our professionals can help satisfy your requirements.
G200 Defense Repair Information Logistics System (DRILS)
TQS developed and currently sustains DoD's web-based G200 Defense Repair Information Logistics System (DRILS) that has been collecting serialized maintenance data for U.S. Air Force aircraft avionics worldwide since 2000. The data collected by DRILS is fed to the Air Force Data Services (AFDS) and Reliability & Maintainability Information System (REMIS) repositories for consumption by users worldwide. G200 DRILS data enhances sustainment support to the warfighter through improved decision support, including root cause analysis and supply chain management.
The flexible design of the DRILS system has withstood the test of time and has proven to be an ideal rapid prototyping environment for Air Force and DoD level initiatives such as Item Unique Identifiers (IUID), warranty tracking, consumption and demand forecasting, performance based contracts, as well as joint service data collection and analysis.
ITEM UNIQUE IDENTIFICATION (IUID)
TQS maintains DoD IUID equipment to its full operational capability, including hardware upgrades and new equipment as necessary. In addition, TQS provides DoD IUID registry support to upload and validate each IUID generated and associated with critical DoD assets.
TQS currently provides full-time and on-site support for 38 IUID production equipment assets at Ogden Air Logistics Complex (OO-ALC), plus two geographically separated unit (GSU) locations. TQS supports the Air Force IUID community by attending, briefing, presenting, training and demonstrating IUID production, marking, and management techniques and principles across the Air Force Sustainment Center (AFSC) and the AF Life Cycle Management Center (AFLCMC). TQS has been supporting IUID Integrated Product Teams (IPTs) since July 2009, helping to improve the processes and expansion of IUID throughout the Air Force.
In addition, TQS created and currently maintains the Defense Repair Information Logistics System (DRILS), also known as G200, a DoD enterprise-wide repair information collection and analysis system based on UID tracking. TQS integrated IUID technology and practices into DRILS years before the mandate for IUID compliance was issued by the DoD.
Product Lifecycle Sustainment Management (PLSM)
- Air Force Material Command (AFMC) Best Practice
TQS performed critical product lifecycle sustainment analyses under the Falcon Flex (FF) and Weapons System Flexible Sustainment (WSFS) contracts supporting the F-16 Supply Chain Manager at Hill AFB. The Air Force Materiel Command (AFMC) F-16 program was the first, and continues to be the leading beneficiary of these sustainment engineering initiatives. Flexible Sustainment utilizes data mining, Pareto analysis, problem isolation, alternatives evaluation, and solution implementation such as Form-Fit-Function and Interface (F3I) or performance-based acquisition to improve system performance. Additionally, PLSM follows the Air Force Smart Operations for the 21st Century (AFSO21) tenet of continuous process and product improvement. Results have shown that restoring reliability and system availability through focused root cause analysis can be achieved in a cost effective manner, increases operational reliability/availability, and save customers millions of dollars each year.
Ref: http://www.au.af.mil/au/awc/awcgate/af/afso21-fact-sheet.pdf
TQS has applied its decades of experience of sustainment engineering to solve some of the DoD’s most enduring avionics frequent failure items (by serial number), a.k.a. “bad actor” problems, by applying critical thinking, robust engineering, and root cause analysis. By finding the true cause(s) of the problem, TQS is able to resolve the mechanical and electrical issue(s) causing some avionics boxes to be very costly “bad actor” outliers in terms of low time-on-wing operational hours compared to other assets in the same part family. This has saved the DoD hundreds of millions of dollars by resolving the issue at the lowest level (in BOM hierarchy and cost) so that an entire expensive avionics asset re-engineering effort is not needed.
Reliability, Statistical Models and Prediction
TQS has matured our statistical and engineering capabilities to support our customers in analyzing their reliability and/or usage data to determine a system’s operational reliability performance in the field. Besides traditional (or classical) statistics, TQS has worked closely with recognized international experts on the use of Bayesian and non-parametric statistics to provide better methods of analyses, particularly for small sample sizes. Given few data points, non-failure data, or you need greater confidence in the outcome, TQS has a solution to meet your needs.
TQS specifically offers an array of Reliability and Statistical Models:
• Design of Experiments (DOE)
• Analysis of Variance (ANOVA)
• Regression Modeling
• Degradation Analysis
• Lifetime Predictive Analysis
• Reliability Block Diagram
• Fault Tree Analysis (FTA)
• Event Tree Analysis (ETA)
• Reliability Allocation and Analyses
• Reliability Growth Analysis
• Bayesian Markov Chain Monte Carlo (MCMC) Simulation Models
• Mean Time Between Failure (MTBF)
• Mean Cumulative Function (MCF)
• Rate of Occurrence of Failure (ROCOF)
DORMANT SYSTEM RELIABILITY PREDICTION SYSTEM (DSRPS)
The Dormant System Reliability Predication System (DSRPS) contract was funded by the Air Force Life Cycle Management Center’s (AFLCMC) Rapid Innovation Fund (RIF) program. The objective of this effort was to provide an accurate LRU-level reliability prediction model/system for dormant weapons systems by developing correct prediction methodologies and prototyping computer software for a wide range of dormant systems. Under this contract, TQS developed an accurate, mathematically correct, Line Replaceable Unit (LRU)-level reliability prediction model for “dormant” weapon systems (using limited test and maintenance data). Military weapons systems, such as missiles, rockets, and bombs are typically one-shot systems that spend most of their lives stored in a dormant state and are required to have high reliability at the time of use.
The DSRPS is a specialized form of an Information Technology (IT)-based Decision Support System (DSS) that enables and performs reliability and statistical types of analyses via Commercial Off-The-Shelf (COTS) tool integration to the maximum extent practicable. It is a comprehensive and interactive software-based system intended to help decision makers compile useful information from raw data, documents, personal knowledge and/or business models in order to identify and solve problems; thus, making better decisions about the product’s performance over its life cycle. The tool enables predictions of dormant sub-systems and LRUs where limited amounts of failure, maintenance and test event data exist. The architecture is designed to quickly facilitate streamlined integration of enterprise data, third party COTS tools and locally generated data.
Key results from this effort were the identification of 10 statistical/reliability model types that Total Quality Systems (TQS) recommended to include in the prototype design of the DSRPS. The model types include 1) Descriptive Statistics, 2) Regression Analysis, 3) Degradation Analysis with Pseudo-Time-To-Failure (PTTF), 4) Reliability Probability Functions and Continuous Distribution Functions (CDFs), 5) Reliability Block Diagram (RBD) Analysis, 6) Fault Tree Analysis (FTA), 7) Event Tree Analysis (ETA), 8) Failure Modes, Effects and Criticality Analysis (FMECA), 9) Reliability Growth Analysis, and 10) Bayesian-Simulation Reliability Analysis.
AN-124 RADAR Sustainability Study
TQS used Isograph’s Reliability Workbench (RWB) software application as the primary tool to calculate reliability predictions for the Short-Range Radar (SRR) and its assemblies and components. Our approach was to build reliability block diagrams and prediction models to determine the impact of the unavailability of spares on system availability. Reliability Workbench provides multiple methods and models for determining current and future reliability of SRR components, subsystems and the overall system. TQS developed a comprehensive build of reliability block diagrams (RBDs) to enable the reliability predictions at the system-to-component levels for the SRR. The RBDs provided cumulative distribution functions (CDFs) for reliability, component-part importance rankings and availability profiles of the SRR and its assemblies and components. TQS was able to quickly and effectively create an RBD framework for the radar system to meet our customer’s needs and timeline.
TQS leverages RWB’s prediction module allowing the use of standardized part libraries for failure rate data. The RWB Prediction Module produces failure rates based on design and operating parameters of the SRR. The prediction module TQS uses provides a variety of failure models that are proven in both industrial and military applications. Some failure models in RWB that TQS uses include: Poisson Failure Model, Stand-by (Redundant) System Failure Model, Time-at-Risk Failure Model and any custom failure model as found necessary. The Poisson Failure Model best described the reliability of the SRR. However, if good historical repair records and usage data are not sufficient to support the creation of defined classical failure distributions, TQS has the expertise to apply Bayesian statistical methods that accommodate scenarios when lack of adequate historical data exists. A best practice Bayesian model is the Markov Chain Monte Carlo (MCMC) simulation model that uses subject matter expertise, engineering knowledge and/or historical data from similar items to build accurate reliability and predictive distributions based on prior information. This model is particularly useful for systems that have sparse failure data, such as dormant systems, and scenarios involving systems and components.
MEAN CUMULATIVE FUNCTION AND RATE OF OCCURRENCE OF FAILURE
Mean Cumulative Function (MCF) is an emerging analysis methodology that has significant feature advantages over the more commonly used Mean Time Between Failure (MTBF) calculation. MCF is a non-parametric graphical estimate of the mean cumulative number of recurrence events per unit versus age, which reveals failure trends and rates at a glance. TQS has developed, documented and demonstrated a process that produces an MCF of unscheduled removal events for a Line Replaceable Unit (LRU). Additionally, TQS has developed, for recurrence data, a Rate of Occurrence of Failure (ROCOF) algorithm that graphically demonstrates the probability of a failure occurring over a given small time interval. Both the MCF and ROCOF analysis processes can be applied to age-based data, as well as calendar date-based data. These analyses use installed operational aircraft flying hours as the “Age” of the LRU.
MCF and ROCOF analyses and results offer metrics for the USAF that exceed the current methods involving MTBF-based metrics. The implementation and application of MCF and ROCOF analysis processes, as a standard method across Air Force Sustainment Center (AFSC) to measure LRU operational reliability in support of weapons system sustainment goals, reveals failure rates and trends in the data and reduces risk in the decision-making processes for the USAF.
Reverse Engineering
To help solve our customers’ obsolete part challenges, TQS has a successful track record for reverse engineering numerous complex electronic and mechanical items. Examples include reverse engineering an obsolete control circuit board for electro-mechanical test equipment, creating usable new tech data for aircraft structural parts, correcting outdated drawings by converting old 2D drawings into modern 3D CAD models, and creating new test fixtures that interface to repair assets.
TQS has the capability and experience for technical and functional analysis of parts, and our engineering staff can physically model 3D designs to allow re-procurement of replacement parts to support continued operations. Our ISO9001/AS9100 processes have created replacement parts that maintain form, fit, function and interface (F3I) of original, but now obsolete, parts. We also provide updated technical documentation of the new parts to the customer to allow for future sustainment, even if the tech data did not exist before. The TQS team has the ability to perform precise 3D scans of physical items and convert them to 3D CAD files to perform virtual fit checks and produce 3D prototypes and/or low-volume production of more complex end items for our customers.
Rapid prototyping is another valuable capability that TQS provides for both internal and external customers. Using the TQS Team’s 3D scanning, 3D CAD and 3D printing capabilities, TQS can rapidly take a concept or idea and create a physical prototype. TQS had successfully made both mechanical and electronic prototypes for aerospace and other applications.
Technical Data Packages
TQS has the proven capability to develop technical data packages for various systems from aircraft to machine guns. Whether it is updating technical maintenance instructions or resolving component drawing issues, we have the expertise to provide a complete package that meet our customer's needs.
TQS provided technical writing and illustration support to the A-10 Engineering Division, Hill Air Force Base. TQS produced source data to incorporate approved repairs into the 1A-10A-3 structural repair manual and other documents as directed by the Government.
TQS was awarded a subcontract by U.S. Ordnance (USO) to support their goal that the M2 machine gun be producible and meet the requirements of the U.S. Army Technical Data Package (TDP). TQS helped resolve conflicts between drawings related to either the high end or low end of specified critical dimensions. These resolutions allowed full interchangeability with parts in the U.S. Government inventory, thus greatly increasing supportability and reliability.
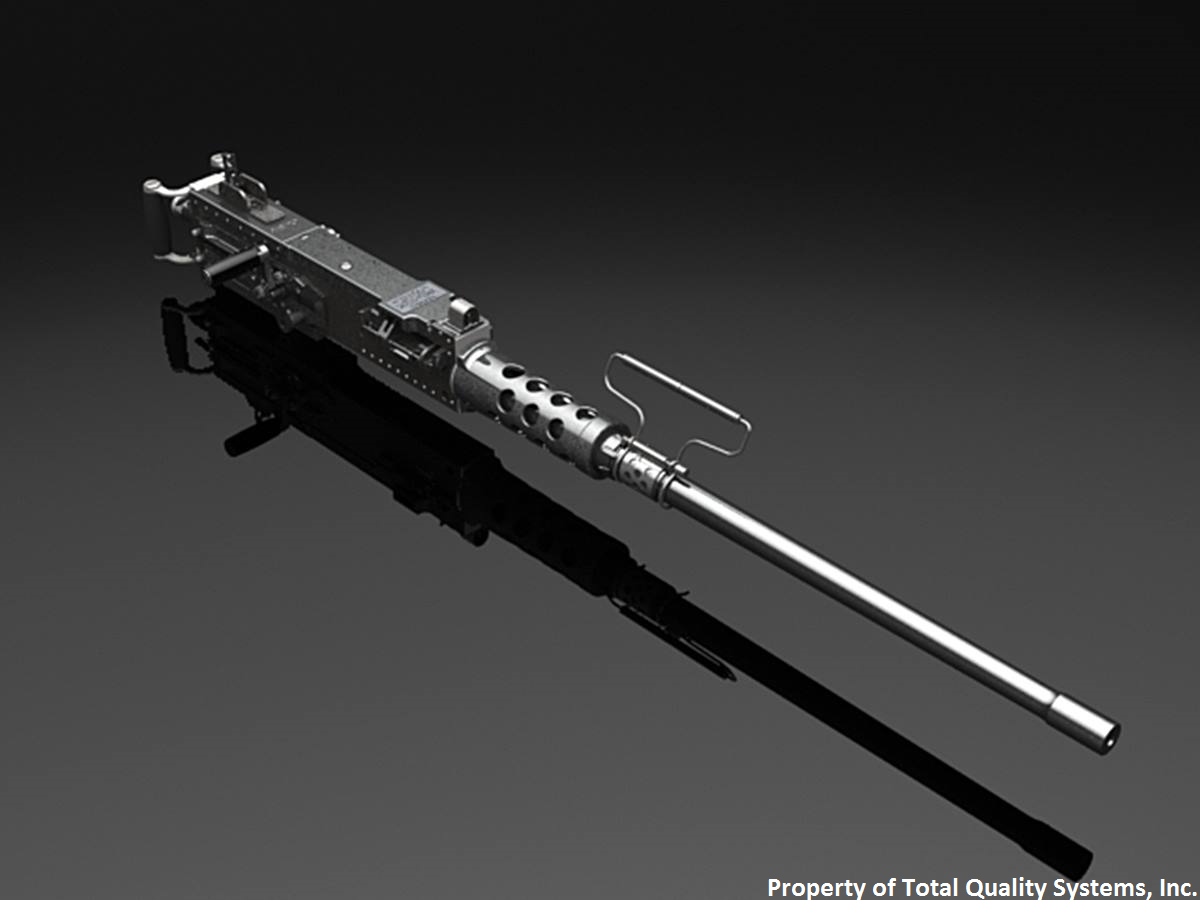